Below is our course on the science of boardology. This text was written circa 2005, when we first started manufacturing our best-in-class aluminum plywood walkboards.
With only minor editing this information holds true to this day, eighteen years later we build essentially the same high-quality walkboard. We still think it’s the best in the business. We hope you’ll take the time to read on, educate yourself, and become a certified boardologist.
We have competitors that offer a light-duty, inexpensive, seven foot aluminum plywood walkboard. We have studied them all carefully. We used to sell the same cheap board they currently carry. We also rented them at our multi-location rental business (a long time ago) and they just would not hold up to those tough conditions.
When renting them, we received numerous returns and complaints from contractors, which led us to manufacture our own board. Unlike other retailers, we don’t simply buy and resell; we actually manufacture. This sets us apart from the competition and ensures that you get more value for your money. Some of these inferior boards are made by companies in the USA or Mexico, but many are imported from Asia.
Here is a picture to help you identify this type of board and make an informed decision.

When you closely examine it, the choice becomes clear. A comparable high-quality board from the major manufacturers will cost you $30 to $80 more. While they produce excellent boards, we believe that ours is superior, and we explain why below.
If you have a few minutes, continue reading to educate yourself on the intricacies and nuances of aluminum plywood walkboards. Afterward, you will be a Certified Boardologist who can differentiate between cheaply made boards and a superior product, thus avoiding buyer’s remorse.
Reasons to buy our board vs our competitors.
Reason 1: Beef
All our metal parts are good and thick. We like to say they’re beefy. Most of our competitors buy boards and then resell them. Those boards often use an I-beam with a wall thickness of approximately .064 inches, compared to our .094 inch wall thickness. With a .064 inch thickness, the beam is so thin that when you screw it to a rib, it can easily compress and dent.
Our competitors assemble these boards in one of two ways: hydraulic press fitting or screwing them together. The hydraulic version is not repairable, and the other is so light duty that it is easily damaged.
Designs like the AP-7 are lightweight boards that contain about four pounds less aluminum than ours, resulting in less strength.
They use thin, inexpensive plywood and rivet it to the aluminum superstructure to regain rigidity. This plywood is often only 11 millimeters thick and contains cheap glue. Some even rivet the plywood on the corner edges because the glue quality is so poor, others paint the edge with sealers to slightly extend the boards lifespan. Sealing the edges makes sense, but it is no replacement for quality materials and construction.
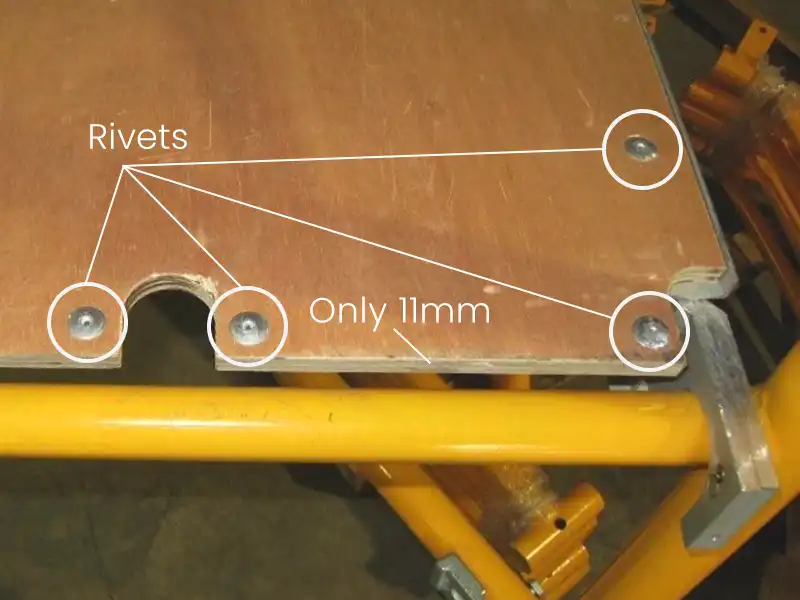
They use two-piece hooks, which clearly distinguish this type of board and should be avoided. When dropped, they are only one quarter the strength of our robust one piece hooks.
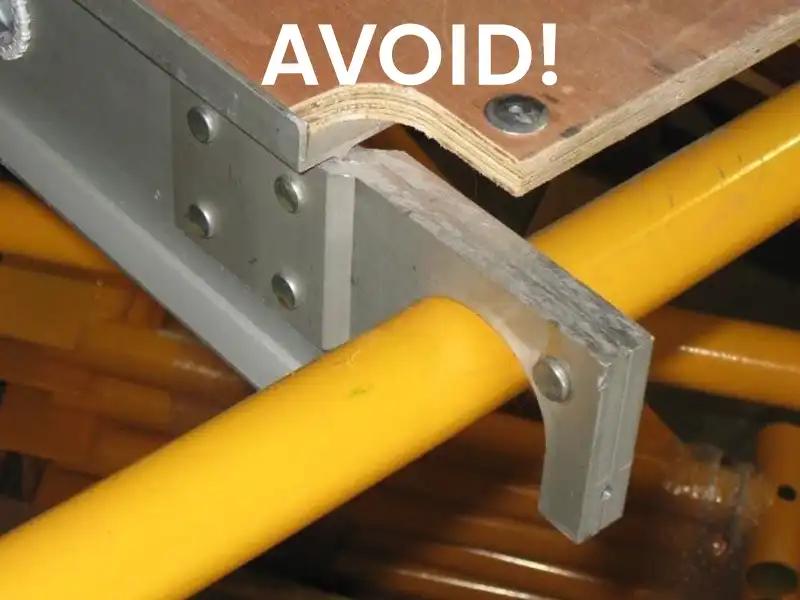
Our hooks, I-beams, and ribs are all substantial and sturdy. The bolts we use are large and we secure them with custom, giant, nylon locking nuts.
Our ribs are patterned after the best designs in the business, with added thickness and increased radius for superior strength. Yes, it costs us more to manufacture our board this way, but we believe it’s worth it.
Everyone wants the strongest walkboard possible underneath them when high in the air on scaffolding.
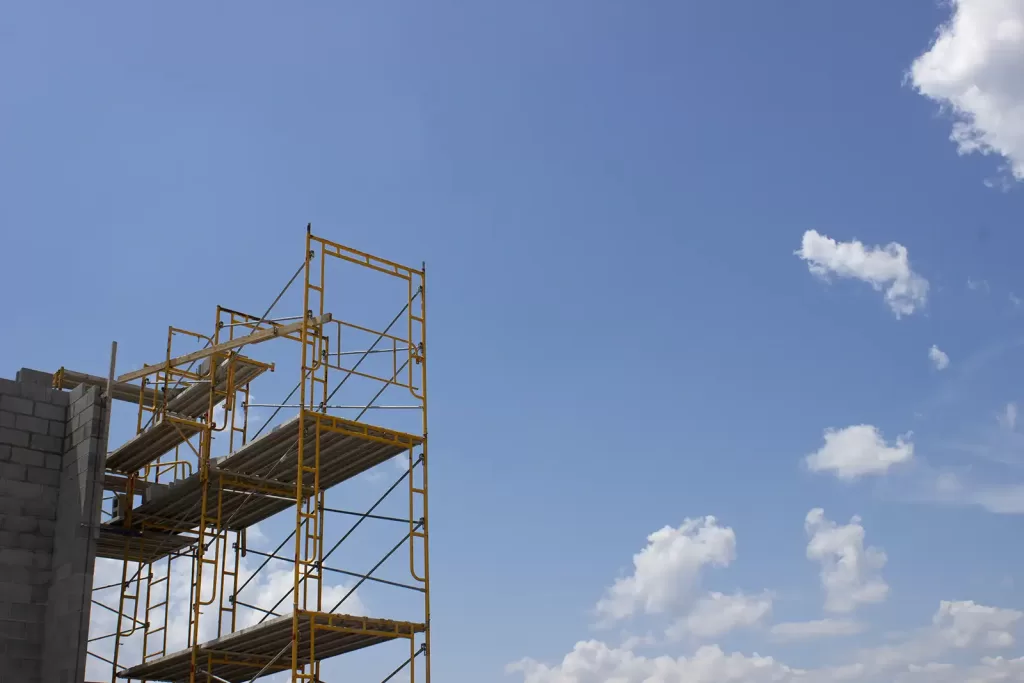
Reason 2: Modularity
Our board is modular — this is very important! Modular means any damaged part can be replaced in minutes. For our boards, this is accomplished with common hand tools.
How modular can a board be when it’s held together with rivets and the support rib tubes are hydraulically pressed together? When you damage that board, what will you do? Well, you throw it away.
It is a major hassle to replace any part on their board. Consider the following scenario:
Say you want to replace the hook. You drill the rivets out, go to the hardware store and buy replacement rivets that you hope will be the same size as the original hole (but probably won’t).
Next you rivet the new hook in place, which will initially be tight from the rivet tool’s tension. You’ll soon find that it goes loose, because the rivets never seem to fit as well after replacement. What a mess!
Worse news is that when someone drops one of these boards, a common occurrence, the hook bends and the main I-beam also deflects. If this happens to you, you’ll wish you had a sturdier, modular walkboard.
Our main beam is so stout that when dropped, it is rarely bent. Why? We were originally a rental equipment company. The boards we rented would often come back in from the field having been dropped rendering them unusable. Our own company’s experience with these poorly designed walkboards, along with customer feedback, is what prompted us to develop a better board.
If you bend our hook, rib, or main beam, it can be replaced in under 10 minutes. The plywood floats in a special slot in the side rail and is replaceable by simply removing three screws. Use a rubber hammer to lightly tap it out of the slot and presto, it’s done! It’s not riveted with eight to twelve rivets, which we learned years ago is a pain.
Our boards are an investment that will last a lifetime. Remember, replaceable or modular is what you want.
Reason 3: Load Rating
Strength: Everyone agrees, it’s best to use the strongest platforms available when standing high in the air on scaffolding.
Our board is load tested to exceed 11,000 pounds (about the weight of an adult African elephant). You probably weigh less than that, so you can imagine it has plenty of capacity. Most other boards are less than a quarter as strong. If you’re comparing our board to any other, ask for their load test results.
Here are our results:
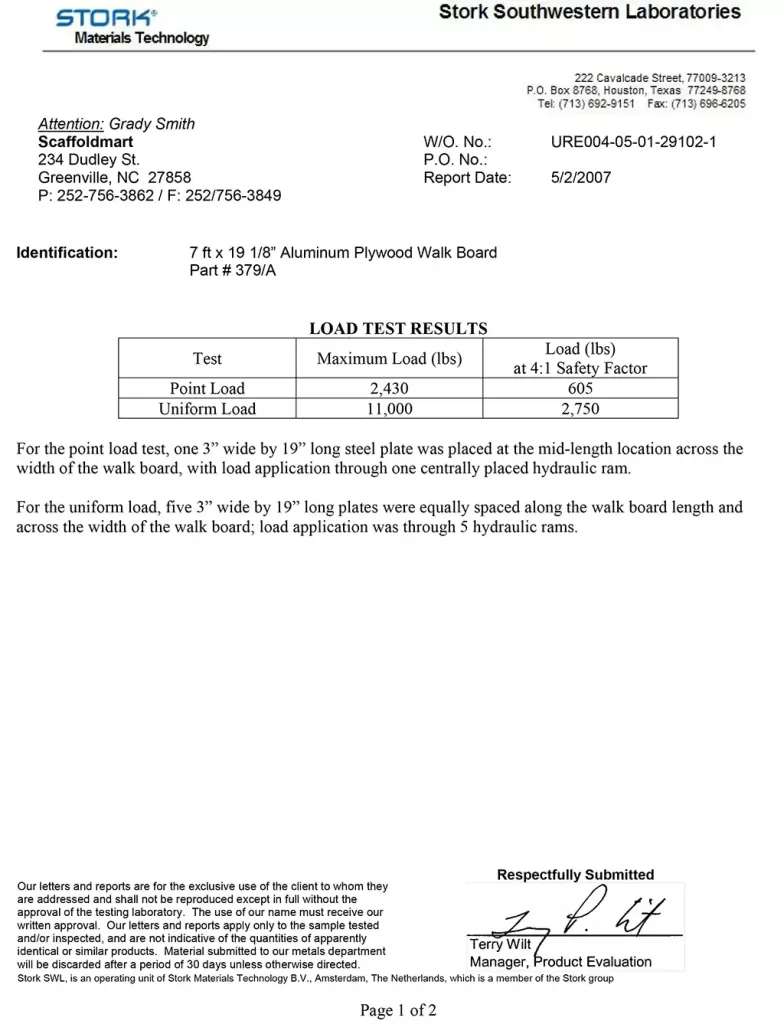
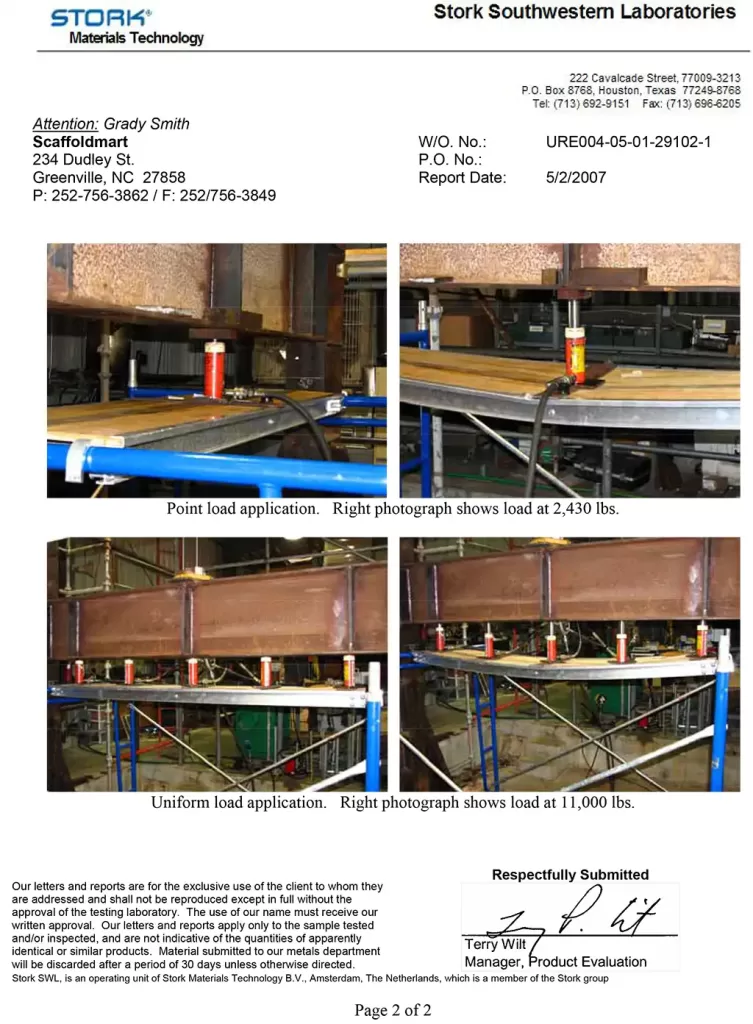
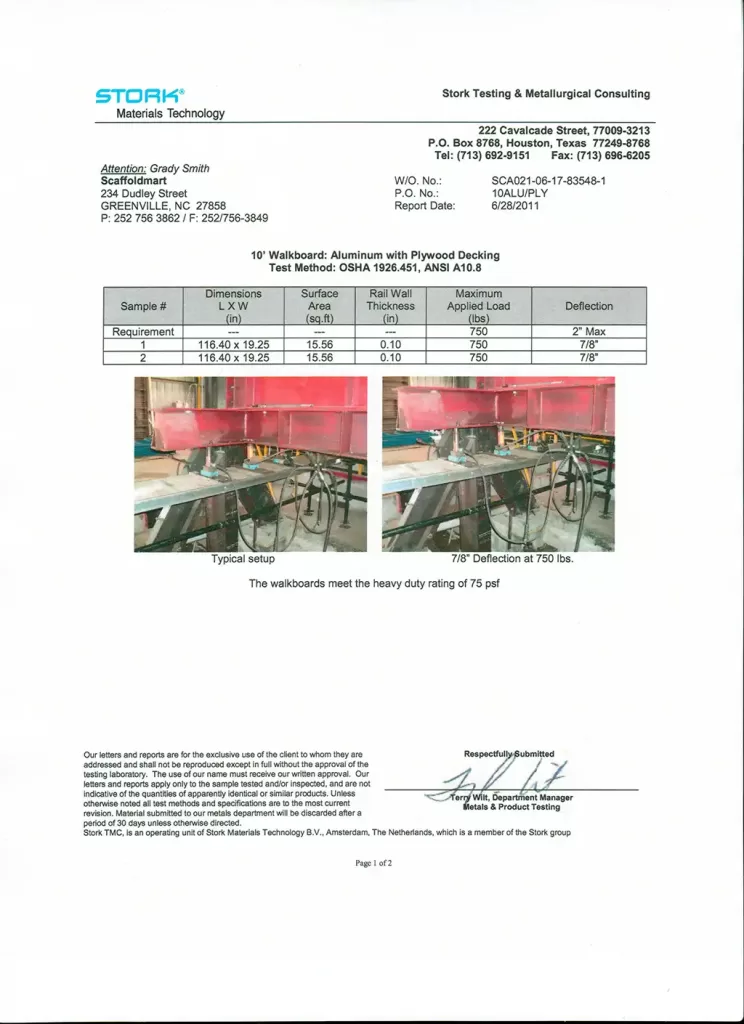
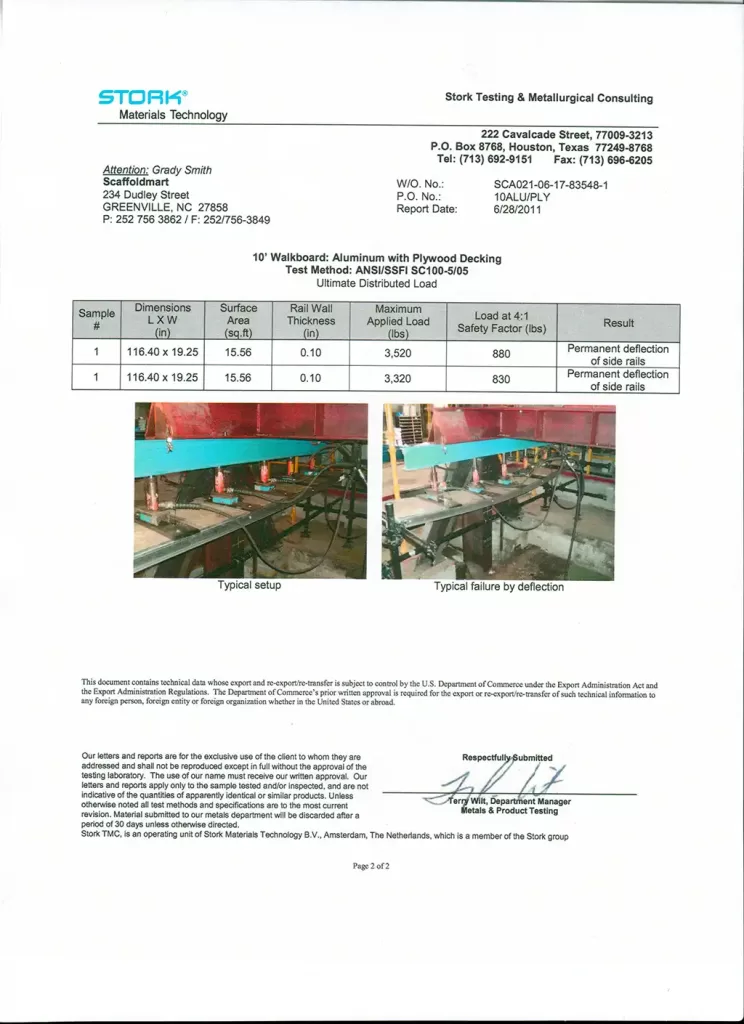
We officially rate our board to align with industry standards to keep customers from pushing the envelope. Rest assured, our board has a safety ratio well in excess of the typical four-to-one OSHA requirement.
Our Board
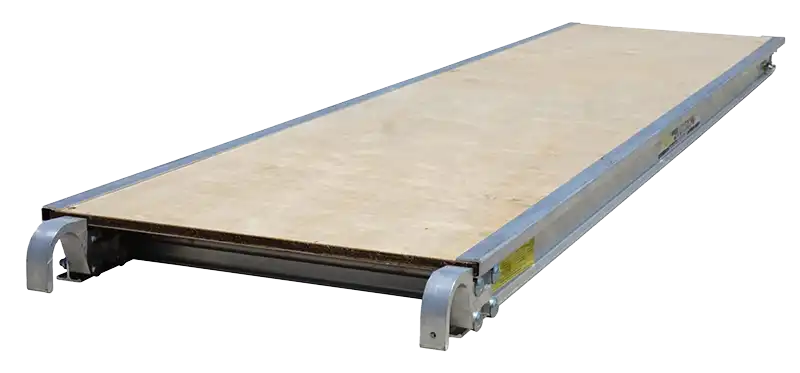
Compare our hook in the following pictures to get a grasp of just how much bigger they are compared to a two-piece hook AP-7 type board. (Our hook is on the top)
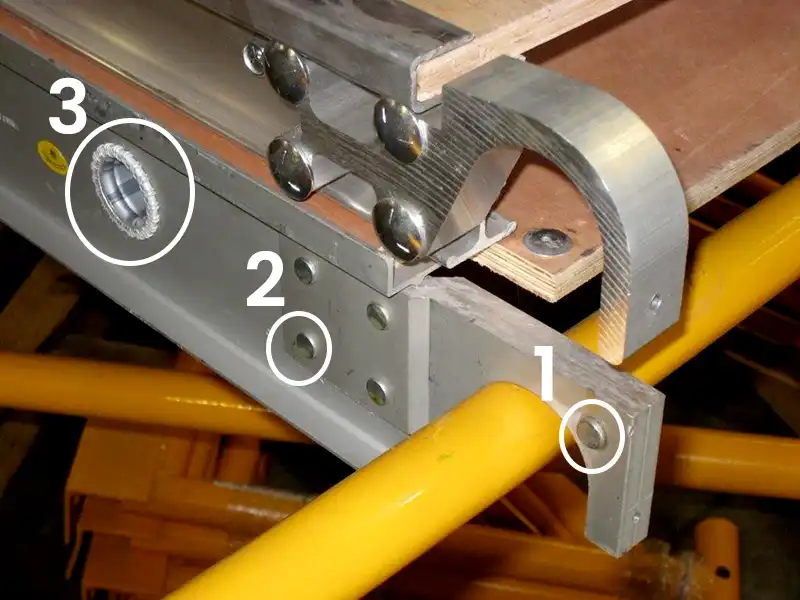
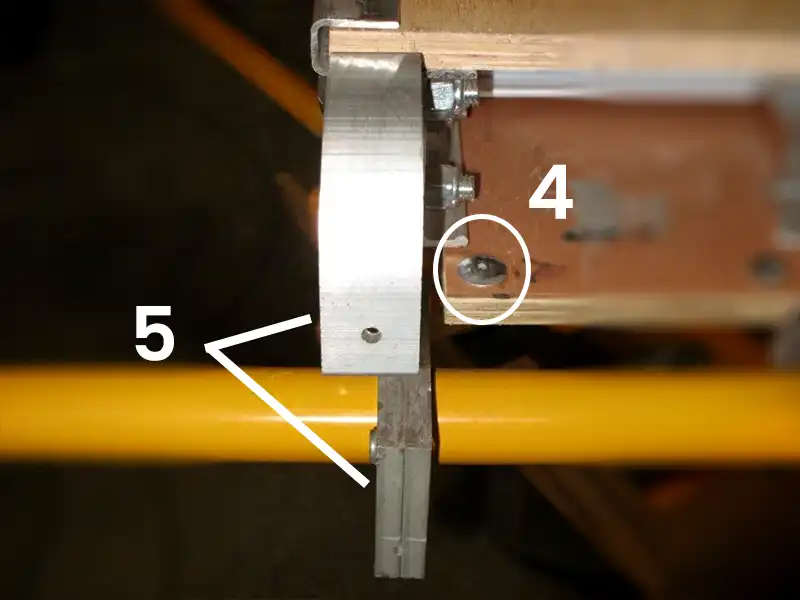
- Notice how the lower hook is held together with one tiny rivet at the end
- Consider how easy it will be to replace ours versus theirs (blots versus rivets)
- Notice the hydraulic press fit of the rib in the picture that makes the main I-beam replacement impossible. If you damage the hook and it affects the I-beam, you have to throw the board away.
- Notice the plywood rivets holding the edges together. This is because rivets are required to boost rigidity since there is so little aluminum in competitive boards.
- Look at the picture that shows the end view of both and see just how much wider ours is than theirs.
There are two types of these cheap boards. The one shown in the photos above and another type which has screws through the main I-beams instead of being hydraulically pressed. Please look at the size difference between their screw (below) and ours in the last couple of pictures.
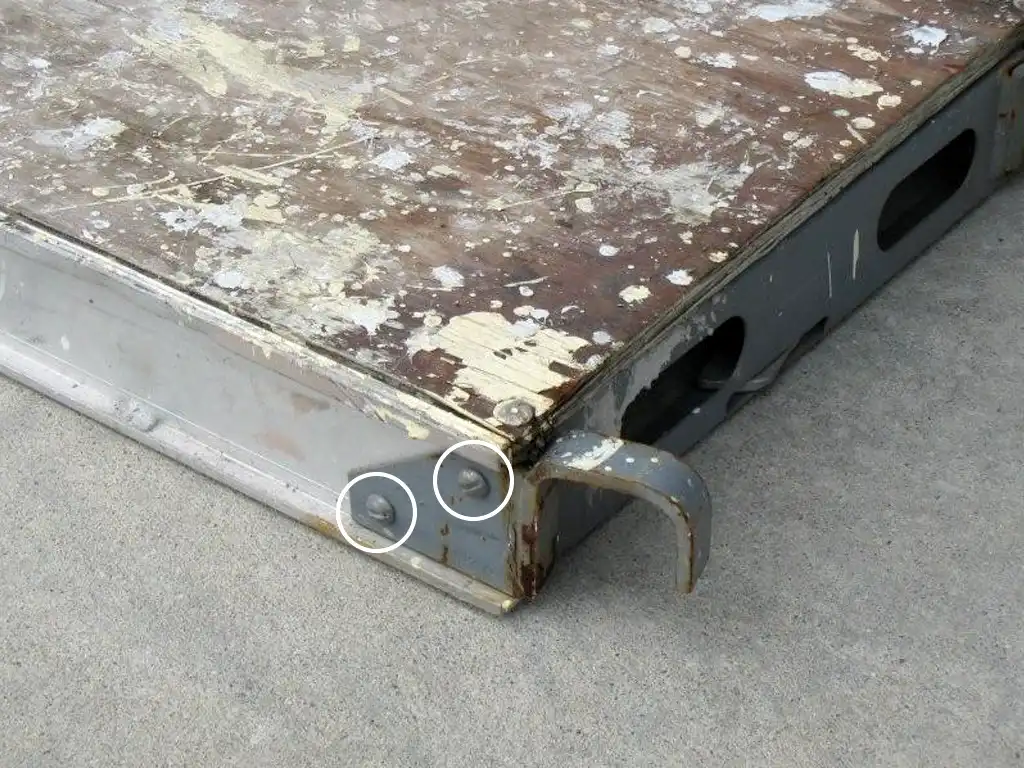
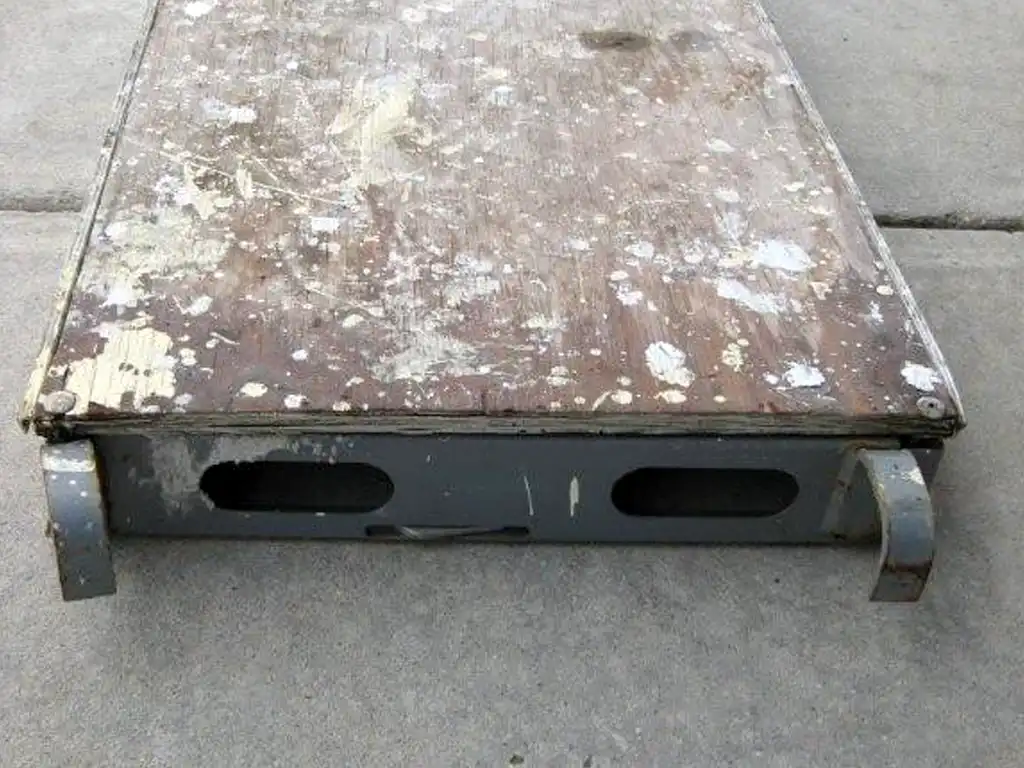
Our competitor’s walkboard
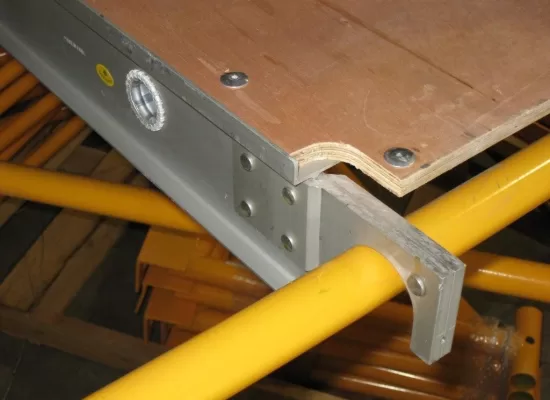
Our competitor’s walkboard: Notice the rivet that holds the two-piece hook together. Notice the wasted aluminum in all the wrong places, not helping strength at all.
Reason 4: Quality Materials
We specify a minimum of seven layers in our plywood for added strength. The more layers, the stronger the plywood will be. The grain pattern of each consecutive layer is turned 90 degrees, which also increases strength.
We measured competitive board plywood thickness, and all the cheap ones are around 11 millimeters. That’s two millimeters less than a full half inch thickness. We specify a sanding tolerance of +/- 0.5 millimeters. This ensures a perfect fit in the aluminum slot and consistent strength.
The glue is fully waterproof, it stays intact after being boiled for 72 hours.
Recently — after years of searching — we found a company headed by third-generation plywood manufacturers. They make their own glue because they do not trust outside suppliers. It’s their own secret recipe and is quite costly. We use it because we wanted to produce the best board we possibly could. One that will resist the weather. If we had cut a corner and gone cheap, we could save three or four dollars per board. We choose to pay more instead.
The seven foot long edge of the plywood is encased in aluminum for complete protection. Replacement of hooks is simply a matter of unbolting and installing a new one. Plywood replacement is even easier. Just remove three bolts and replace the plywood in a few minutes. Slide it right out and slide another right in.
This forethought concerning serviceability protects your investment. Compare us to any board anywhere. We think you will agree… stronger, safer, waterproof glue, the strongest hooks… it’s better.
Reason 5: Honest Business
We shoot straight. We’re family owned and operated. We design our products ourselves with a small, tight-knit team.
At this point, we’ve been in the business two decades, always taking pride in what we do. We relate to the struggles and triumphs of doing-it-yourself and hard, honest work. We make mistakes, but we will always make it right… in fact, we guarantee it!
This text was written specifically to help you discern a good aluminum plywood walkboard from a bad one. It reflects a time when our business was young, and we were learning. We have grown, expanding our team and product line, but our approach is the same. That approach informs everything we do to this day, and it’s why we decided to republish this updated version of the Course on Boardology. Thank you for reading.
If you made it this far you are officially a Boardologist. We’d bet you now know more about aluminum plywood walkboards than 99 percent of the world’s population. We obsess over these details to bring you the best scaffolding products we can. We hope you have found some value, and never buy a two-piece hook!